×
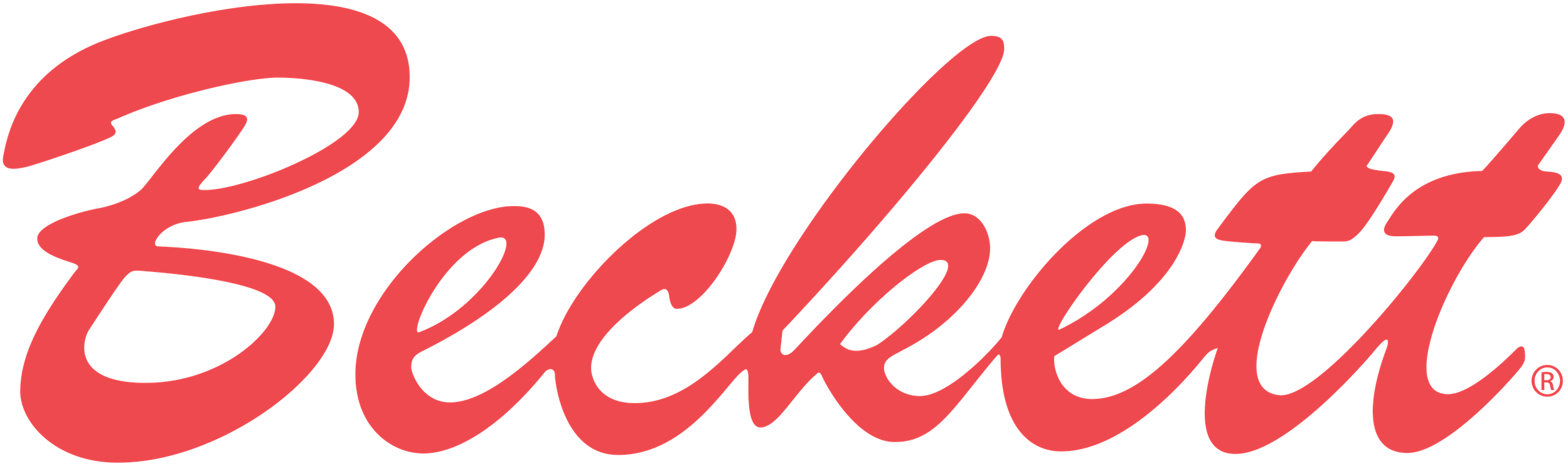
Regional Sales Manager Request
Please fill out the form below to contact Beckett directly and we’ll get back to you within 24 hours.
Action: Check voltage between L1 and L2 terminals. See the GeniSys Manual for details.
Additional Action: If no voltage is present, check voltage at the operating limit.
Action: Verify:
Action: Jumper TW and TR of the Primary Control. If the burner starts, then check your thermostat.
Additional Action:Also verify there is 120v at L1 to L2 and Limit to L2.
Action:
Additional Action: If the light remains on:
Notes: See the Cad Cell Tech Bulletin for more information.
Action: Press and hold the reset button for at least one second. This will reset the control. For more in-depth GeniSys troubleshooting, visit the System Controls GeniSys Series 7505, 7575, 7580 Troubleshooting section.
Notes: The GeniSys Primary Control may lock out for:
See the Cad Cell Tech Bulletin for more information.
Action:The Genisys Primary Control is in a Restricted (hard) lockout This means the control has locked out 3 times.
Additional Actions:Hold the reset button down for 15 seconds. When the reset light goes out, release the button. The control will reset. For more in-depth GeniSys troubleshooting, visit the System Controls GeniSys Series 7505, 7575, 7580 Troubleshooting section.
Notes:The pump prime light will turn on solid once the button is held for 15 seconds until the button is released. Refer to your GeniSys manual for more information. To help troubleshoot the GeniSys control more effectively, use our Contractor’s Tool (Part number 52082U).
Action: Check and correct flame sensing circuit (cad cell and wiring).
Notes: See the Cad Cell Tech Bulletin for more information.
Action: Verify burner specs.
Notes: Refer to our Residential Oil Specification Guide to see start up settings.
Cause 3 – Flame failure
Action: Check and correct:
Notes: Refer to our Residential Oil Specification Guide to see start up settings.
Cause 4 – Lack of retention
Action:
Notes: For more information about the Low Firing Rate Baffle (click here).
Action: Bleed pump, Check for air in oil supply line by putting a clear hose on the pump bleeder port.
Notes: Refer to the Nozzle Afterdrip Tech Bulletin for more information.
Action:
Notes: Refer to the Nozzle Afterdrip Tech Bulletin for more information.
Action: Loosen 1/8″ high pressure copper line and if oil is leaking through, replace valve or pump with solenoid valve.
Notes: Refer to the Nozzle Afterdrip Tech Bulletin for more information.
Action: Check and correct:
Notes: Refer to our Residential Oil Specification Guide to see start up settings.
Action: Pre-set air settings are approximate for start-up. Refer to the appliance manual for recommended set-up procedure.
Notes: Refer to our Residential Oil Specification Guide to see start up settings.
Refer to our Residential Oil Specification Guide to see start up settings. Reference NFPA 31 Standard for the Installation of Oil-Burning Equipment.
Action: Check and correct:
Notes: Refer to the Combustion Air Requirements Tech Bulletin for more information.
Action: Replace nozzle.
Notes: Refer to our Residential Oil Specification Guide to see start up settings.
Action: Run a vacuum test, Use a clear hose on the pump bleeder port to see if there is air present.
Notes: Refer to the Suction Line Leaks Tech Bulletin for more information.
Action: Refer to the Appliance manual.
Notes: Refer to our Residential Oil Specification Guide to see start up settings.
Action: Check chamber and breech draft.
Notes: Refer to the Appliance manufacturer for recommended draft settings.
Action: Test with alternate source of fuel.
Notes: Refer to the Oil Quality Tech Bulletin for more information.
Action: Replace chamber.
Action: Check nozzle, draft and combustion chamber.
Action: Verify your components are correct.
Notes: Refer to our Residential Oil Specification Guide to see start up settings.
Action: Check for air in the fuel supply line. Bleed the oil pump.
Additional Action: If noise persists, put on a vacuum gauge at the fuel pump’s inlet to see if there is a restriction in the oil supply line.
Notes: For additional potential causes, see our technical bulletin for Locating Suction Line Leaks.
Action: Replace Motor.
Action:
Notes: Refer to the burner manual for the proper gap of the blower to motor flange surface.
Cause 1 – No power to burner
Action:
Correct power supply.
Notes:
RM7800 Display Module is available for more in depth troubleshooting codes. (Part number 7542U).
Action:
Wire the control as shown on the schematic (110 v control power is generally separate from high voltage motor power).
Notes:
The basic wiring schematics are located in the appropriate burner’s manual. Refer to the manuals for each burner for more information.
CG15 Gas Burner | 560 to 1,500 MBH | AC Power
CG25 Gas Burner | 990 to 2,700 MBH | AC Power
CG50 Gas Burner | 1,400 to 5,000 MBH | AC Power
Action:
Replace fuse.
Action:
Verify the control is receiving voltage.
Notes:
Replace flame safeguard.
Action:
Trace limit string with multimeter and correct.
Notes:
Verify there is 120v to terminals L2 and 6 on the subbase of the control.
Action:
Check and correct blower motor condition.
Action:
Replace flame safeguard.
Action:
Replace flame safeguard.
Notes:
Examples are: Resistors JR1, JR2 and JR3.
Action 1 – CG10 Burner Models:
When the limit string is complete, 120v is sent from terminal 5 of the controller subbase to the blower motor. Verify that voltage is present. If voltage is present:
Action 2 – CG15, CG25 and CG50 Burner Models:
When the limit string is complete, 120v is sent from terminal 5 of the controller subbase to the motor contactor coil. Verify that voltage is present. If voltage is present:
Additional Action:
Is jumper JR3 of RM7897 clipped? If so, check and correct: power supply to blower motor, control signal to starter or contactor, overload trip.
Notes:
Is JR3 intact? Burner would not have locked out.
Action:
Check and correct ignition and fuel valve wiring, re-set flame safeguard.
Action:
Check furnace for flame or stray UV source (bright light or spark) – correct and re-set flame safeguard.
[/column][/column-group] [column-group][column]
Action:
Is jumper JR3 of RM7897 clipped? If so, check and correct blower motor condition. If not, burner would not have locked out.
Action:
Replace purge card, re-set flame safeguard.
Action:
Check and correct electrical power supply, re-set flame safeguard.
Action:
Check and correct POC switch, adjustment and wiring. Re-set flame safeguard.
Action:
Is jumper JR3 of RM7840L clipped? If so, check and correct all interlocks for correct status (at least one failed). If not, this does not apply.
Action:
Replace flame safeguard.
Action:
Has jumper JR3 been clipped? If so, burner would have locked out after 10 seconds of not proving air flow.
Notes:
Is jumper JR3 Intact? If so, burner would have locked out after 4 minutes of not proving air flow. Check and correct blower wheel, air switch sensing lines, wiring, and air switch setting.
Action:
Change switch position to run.
Notes:
This is located on the top of the 7800 Control.
Action:
Replace flame safeguard.
Action:
Check and correct ignition transformer, high tension wire, electrode settings, flame safeguard ignition circuit and wiring.
Notes:
The flame establishing period is 4 seconds. If no spark is present during this period, replace the ignition transformer. Part number 51976U (CG15, CG25 and CG50). Part number 52014U (CG10).
Action:
Check and correct manual and electric valves in gas train, gas supply to train.
Action:
Check furnace for flame or stray UV source (bright light or spark) – correct.
Action:
Observe the furnace for flame. If present: check and correct flame rod or scanner, amplifier and wiring; for flame rod, verify grounding of flame rod circuit at sub-base.
Notes:
Observe the furnace for flame. If not present: check and correct fuel supply and gas train (including length from last valve to manifold), air settings, draft and blower, and ignition system and electrodes.
Action:
Check and correct ignition and fuel valve wiring.
Action:
Replace purge card, re-set flame safeguard.
Action:
Is the control RM7840L (or RM7897 with jumper JR3 clipped)? If so, check and correct blower wheel condition and tightness, air switch function, wiring and setting. If not, burner would not have locked out.
Action:
Check and correct damper travel is unobstructed, damper motor end switch setting, wiring.
Action:
Check and correct damper motor end switch wiring.
Action:
Check and correct POC switch, adjustment and wiring. Re-set flame safeguard.
Action:
Replace flame safeguard.
Action:
Check and correct flame sensing circuit – flame rod or scanner, amplifier and wiring. For flame rod, verify grounding of flame rod circuit at sub-base.
Action:
Check and correct fuel supply, air damper settings, blower wheel and motor, furnace draft
Notes:
Refer to our Commercial Gas Specification Guide to see start up settings.
Action:
Check and correct power supply to burner.
Action:
Check and correct power supply to burner, re-set flame safeguard.
Action:
Check and correct ignition wiring, re-set flame safeguard.
Action:
Replace purge card, re-set flame safeguard.
Action:
Is the control RM7840L or RM7897 with jumper JR2 clipped? If so, check and correct:
Action:
Is the control RM7840L or RM7897 with jumper JR2 clipped? If so check and correct:
Action:
Is control RM7840L (or RM7897 with jumper JR3 clipped)? If so, check and correct blower wheel condition and tightness, air switch function, wiring and setting. If not, burner would not have locked out.
Action:
Check and correct air damper motor low fire switch and wiring, and air damper obstruction.
Action:
Replace flame safeguard.
Action:
Check and correct: POC switch, adjustment and wiring. Re-set flame safeguard.
Action:
Check and correct: ignition and fuel valve wiring, re-set flame safeguard.
Action:
Replace purge card, re-set flame safeguard.
Action:
Trace power through rate control wiring to determine where power is lost – flame safeguard terminal – burner low fire switch – boiler rate control switch(es) – low air relay – correct as required to power damper motor.
Action:
Check for binding in damper – replace damper motor if required.
Action:
Verify correct wiring, replace flame safeguard.
Action:
Trace power through fuel valve wiring to determine where power is lost – from flame safeguard to damper motor – damper motor switch – fuel valve wiring – correct as required to power fuel valve.
Cause 2 – High fire fuel valve is powered but fuel pressure does not increase
Action:
Check high fire fuel pressure regulator setting – if it’s correct replace the high fire fuel valve.
Action:
Check and correct: wheel set screw tightness, wheel-to-motor plate and wheel-to-inlet guide clearances, wheel integrity.
Action:
Check and correct: damper obstructions, damper blade tightness on shaft, low fire firing rate (too low causes noise).
Action:
Check and correct: firing rate (too high causes noise), O2 level (excessive air causes noise), head setting adjustment.
Action:
Check and correct:
Action:
Check and correct: Draft is too high (tall stack, inadequate draft controls), lightoff rate is too high (check manifold pressure at light-off), ignition electrodes are worn or incorrectly set, incorrect burner head and/or head setting, high excess air, incorrect application (furnace too small), “feedback” resonance from stack (add a barometric).
Acton:
Slight trumpet (barely audible, lasts < 5 seconds) is considered a normal condition, don’t worry about it. Pronounced trumpet – treat as rumble or roar.
Action:
Check and correct lockout condition.
Acton:
DO: Call your gas supplier from a phone outside the building and follow his instructions. Call the fire department if you cannot contact your supplier.
DO NOT touch any electrical switch, try to light any appliance, or use any phone in the building.
Action:
Take corrective action gradually to avoid explosion hazard. Check for not enough air or too much gas: inadequate air supply to boiler room, obstructed or incorrectly adjusted air inlet to burner, blocked or incorrectly adjusted stack vent, excessive gas pressure to train, seized or incorrectly adjusted gas pressure regulator.
Action:
Check that blower is tight on motor shaft, has no missing balance weights, no obvious damage to blower wheel.
Action:
Check and correct: excess air level, head setting, gas spud obstruction, correct blower wheel size, supply pressure to gas train (high or very low pressure drop across regulator), pressure fluctuations coming to gas train from oversized supply regulator, pressure fluctuations coming to furnace from flue stack (add a barometric), un-approved boiler application (furnace too small).
Action:
Check and correct: excess air is low (low O2 or high CO2), rate is high, operation at high elevation (flame expands in low barometric pressure), flue gas recirculation, cold furnace.
Action:
Check and correct: excess air is high (high O2 or low CO2), rate is low, furnace has a lot of refractory (re-radiated heat speeds up flame and shrinks its size).
Action:
Check and correct: burner head not centered in air tube, gas orifice obstructed, furnace flow pattern (flame drawn toward furnace outlet), furnace refractory pattern (re-radiated heat from refractory speeds up flame), flame buoyancy in furnace (greater influence in cold furnace).
Action:
Always use properly calibrated instruments to set combustion. Some yellow in flame is normal. Yellow flames could indicate fuel composition has changed (gas utility injects propane into natural gas for low ambient conditions), low excess air, use of FGR to reduce NOx, reduced mixing rate (head setting too far open).
Action:
Always use properly calibrated instruments to set combustion. Reddish blue flames could indicate higher than normal firing rate, or normal firing in a refractory lined chamber.
Action:
Normal condition for all of our “step spud” burners (all models offer this design). Only our CG10.1 through CG10.3 offer a swirling flame, and the swirl level in that design is small.
Action:
Normal CO for cast iron boilers is less than 50 PPM, and usually 10 PPM or less at high fire. If greater, check and correct: excess air (O2 or CO2), burner head selection and setting, insertion depth in short furnaces, flame impingement on damaged refractory, high draft (pulling partially burned products from the base of the flame), missing or damaged O-rings on the gas gun, cold furnace, greatly oversized furnace.
Action:
Specified damper opening is a guideline for start-up; don’t be afraid to change it. Normal O2 at high fire is 3 to 4% (CO2 is 9.5 to 10%). If less O2 (more CO2), check and correct: adequate air supply to boiler room, boiler furnace pressure, firing rate (preferably by clocking a meter, but also compare to data in burner manual), calibration of analyzer, burner head selection and setting.
Action:
Specified damper opening is a guideline for start-up, don’t be afraid to change it. Normal O2 at low fire is 4 to 5% (CO2 is 8.9 to 9.5%). If more O2 (less CO2), check and correct: stack draft (barometric control is recommended for stacks over 10′ tall), firing rate (preferably by clocking a meter, but also compare to data in burner manual), calibration of analyzer, burner head selection and setting.
Cause 4 – O2 (CO2) – outside specified range during modulation
Action:
The burner manual has a section devoted to modulation adjustments – work from it.
[/column][/column-group] [column-group][column]
Action:
Changes of about 1% O2 (0.5% CO2) are normal. They are caused by changes in fuel properties (utilities change gas properties in response to available supplies and outdoor temperature), air density changes (barometric pressure, temperature, moisture content), and boiler draft changes (outdoor temperature and wind conditions). If O2 (CO2) changes exceed 1% look for mechanical problems with fuel pressure regulation, draft control, or the burner’s blower and damper systems. A service log of burner settings and performance is recommended.
Action:
Check and correct: incoming gas pressure at rate, full open position on all manual valves, pressure drop across each SSOV, debris in gas line.
Action:
Check and correct: adequate ventilation to support all boiler room equipment, high furnace pressure, burner head setting, full opening of burner air damper, debris obstructing air damper, correct air guide or inlet sleeve, blower wheel not tight on motor shaft, correct blower wheel adjustment, combustion air leakage from burner, scroll extension in place in CG10, correct 3 phase motor rotation, blower wheel damage.
Action:
Clock firing rate and adjust gas pressure regulator for higher pressure.
Action:
Verify correct regulator / adjustment spring selection, gas train selection, gas train component pressure drops, supply pressure to the gas train (at rate).
Action:
Check and correct: high draft (no barometric?), breech damper too far open, low boiler draft loss (missing spinners / turbulators / baffles).
Action:
Check burner head identification and orifice sizes.
Action:
Clock firing rate and adjust gas pressure regulator for lower pressure.
Action:
Verify correct regulator / adjustment spring selection.
Action:
Check and correct: low draft (stack size?), breech damper too far closed, high boiler draft loss (incorrect spinners / turbulators / baffles, dirty boiler), flue gas analysis (high O2?).
Action:
Check burner head identification and orifice sizes.
Action:
Check your incoming voltage to L1 and L2.
Notes: Refer to your GeniSys manual for more information. To help troubleshoot the GeniSys control more effectively, use our Contractor’s Tool (Part number 52082U).
Action: Verify:
Notes: Refer to your GeniSys manual for more information. To help troubleshoot the GeniSys control more effectively, use our Contractor’s Tool (Part number 52082U).
Action:
Notes: Refer to your GeniSys manual for more information. To help troubleshoot the GeniSys control more effectively, use our Contractor’s Tool (Part number 52082U).
Action:
Notes: Refer to your GeniSys manual for more information. To help troubleshoot the GeniSys control more effectively, use our Contractor’s Tool (Part number 52082U).
Action:
Press and hold the reset button for at least one second. This will reset the control.
Additional Actions: The Genisys Primary Control may lock out for:
For more possible causes, see the “Troubleshooting an Oil Burner” tech bulletin.
Notes: Refer to your GeniSys manual for more information. To help troubleshoot the GeniSys control more effectively, use our Contractor’s Tool (Part number 52082U).
Action:
The Genisys Primary Control is in a Restricted (hard) lockout This means the control has locked out 3 times.
Additional Actions:
Hold the reset button down for 15 seconds. When the reset light goes out, release the button. The control will reset. For more possible causes, see the “Troubleshooting an Oil Burner” tech bulletin.
Notes: The pump prime light will turn on solid once the button is held for 15 seconds until the button is released. Refer to your GeniSys manual for more information. To help troubleshoot the GeniSys control more effectively, use our Contractor’s Tool (Part number 52082U).
Action:
Notes: Refer to your GeniSys manual for more information. To help troubleshoot the GeniSys control more effectively, use our Contractor’s Tool (Part number 52082U).
Action:
For possible causes, see the “Troubleshooting an Oil Burner” tech bulletin.
Notes: Refer to your GeniSys manual for more information. To help troubleshoot the GeniSys control more effectively, use our Contractor’s Tool (Part number 52082U).
Informative and technical training resources from the leading experts in the heating industry
Have questions about our products? Looking for a solution to address a particular application? Looking to improve the overall productivity and profitability of your operation? Please don’t hesitate to reach out or schedule a no obligation, 1-on-1 consultation with a Beckett Technical Specialist — we’d love to help.
Beckett solutions are available through our network of Distributors, Independent Representatives, and Export Representatives all around the world.