×
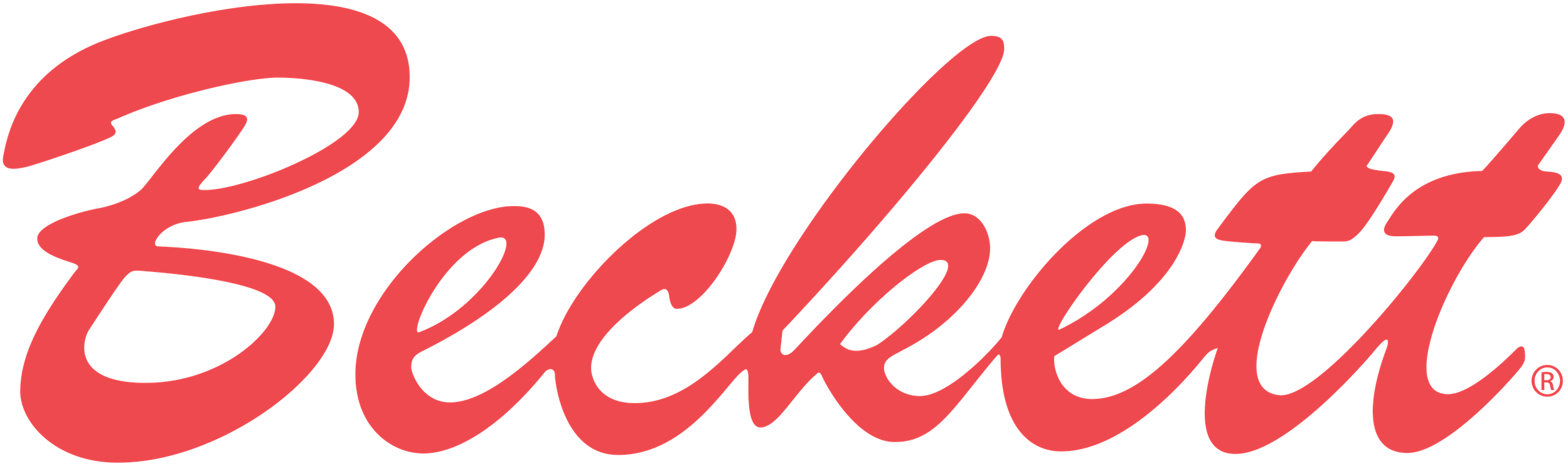
Regional Sales Manager Request
Please fill out the form below to contact Beckett directly and we’ll get back to you within 24 hours.
In March of 1993, Beckett released a technical bulletin entitled, “Burner Motor Service Facts” which addressed basic operation and service of the split phase motor used on the Model AF and AFG oil burners. As a companion to that bulletin, this bulletin will discuss operation and troubleshooting of the permanent split capacitor (PSC) motor available for all burners requiring a “NEMA M” flange.
An oil burner motor has two windings, oriented 90° to each other. The windings are designed so that the current in one lags the current in the other. This difference makes the resulting magnetic field rotate, creating a torque that turns the motor shaft.
After a split phase or cap start motor is started, a centrifugal switch on the shaft opens, disconnecting the start winding or capacitor. The motor then runs using only the run winding. See the simplified circuit diagram on the following page. | A PSC motor uses a capacitor (a device that can store and release electrical charge) in one of the windings to increase the current lag between the two windings. Both the capacitor (auxiliary) winding and the main winding remain in the circuit the entire time the motor is running, hence the name “permanent.” |
TEST PARAMETER | SPLIT PHASE | PSC | COMMENTS |
Average starting current (locked rotor current) | 15 – 25 Amps | 7 Amps | PSC has a decreased starting current, which extends relay and switch life. |
Average running current | 2.0 – 2.4 Amps | 1.5 Amps | PSC draws an average 30% less current. |
Approximate starting torque | 55 – 70 oz-in | 49 oz-in | Pump starting torque requirement 13 – 20 oz-in. |
Average electrical power | 200 Watts | 170 Watts | PSC draws an average 15% less power. |
Efficiency | 40 – 50% | 60 – 65 % | Efficiency = output power (mechanical) divided by input power (electrical) |
AFG full load speed | 3375 – 3450 rpm1 | 3440 – 3460 rpm1 | PSC: Similar or increased output power. |
1 Rule of thumb: Air flow (cfm) is proportional to motor speed, and static pressure varies with the motor speed squared (if the speed increases by 2%, the pressure increases by 4%).
The PSC motors tested above perform with increased efficiency, equal or increased power output, and lower starting and running current than the split phase motors. PSC motors also have the advantage of having fewer moving parts (no end switch), which enhances its reliability.
The AFG burner motor’s mounting flange is commonly called an M flange. “M” is a NEMA (National Electrical Manufacturers Association) code for this style of motor mounting, enabling any motor with this designation to be mounted to any other burner that requires this style of flange. N is the NEMA code for the larger mounting flange (for instance, for Beckett “S” chassis burners). Some motors have cooling holes in the flange, and some flanges are totally closed. If the blower wheel does not cover the cooling holes when the wheel is installed, too much air can leak through the holes, decreasing the static pressure and possibly affecting burner performance.
Most UL recognized oil burner motors have an internal thermal protector that turns off the motor if it gets too hot. The Beckett PSC employs an automatic reset thermal protector that will reset by itself after an event that causes it to open.
NOTE: Applications in which the ambient temperature exceeds the maximum 150°F rating of the motor may cause the protector to trip, so keep those doors open on enclosed trailers and vans with generator skid units installed in them.
Sleeve bearings, also called bushings, are special metal sleeves around the rotor shaft. Oil is applied between the shaft and the sleeve, lubricating the shaft and allowing it to turn with little friction due to the thin film of oil (similar to skating on a thin film of water while ice skating). Many modern sleeve bearings are permanently self-lubricated and have a sponge-like material that continually supplies oil as the rotor turns. Sleeve bearings require increased starting torque since the rotor must turn at near rated speed in order to distribute the lubricating oil properly.
Permanently lubricated, shielded ball bearings are better sealed to keep out dirt and water, promoting long life. Less rolling resistance delivers more power to the load. The press fit to the motor shaft eliminates end play, keeping the gap between the blower wheel and the housing constant, minimizing air leakage and increasing the zero-flow static pressure as much as 0.3 to 0.4 inches water column compared to sleeve bearing motors, for cleaner starts (less soot).
PSC motors have two major areas to troubleshoot: the capacitor and the windings. Both are relatively simple to check and require only an analog ohmmeter.
CHECKING CAPACITORS. A failed capacitor will cause a PSC motor to either stop or run more slowly than designed, and the thermal protector will trip if a restart is attempted. To check a capacitor, perform the following steps:
Good capacitor: ohmmeter reading should jump immediately down scale, and then quickly increase again to infinity.
Bad capacitor: If the meter settles at zero ohms, the capacitor has short-circuited. If the meter resistance is infinite the entire time, the capacitor has open circuited. A failed capacitor must be replaced by one with the same capacitance (microFarads or μF) and a voltage rating at least as great as the original one.
For the Beckett PSC motor, from L1 you should have measured 3-6 Ohms and
14-18 Ohms. From L2 you should have measured a short (<1 Ohm) and 17-24
Ohms. If you do not observe these resistances, the motor windings are faulty,
and the motor should be replaced.
“Dead spot” is a common term for a certain orientation of the rotor at which the motor (PSC or split phase) will not start. Two things can cause dead spots. First, if the start switch of a split phase motor is unevenly worn, the contacts may become slightly separated if the rotor is in a particular location. No current will be able to flow through the start winding, and the motor will not start. Secondly, there could be a break in one of the aluminum bars inside the rotor, due to a fault in the casting process. If this occurs and the rotor happens to be in that particular spot when the motor is turned on, the motor may not have enough torque to start the burner. This fault in the rotor is quite rare, and cannot be repaired.
PSC MOTOR TROUBLESHOOTING
CONDITION | CAUSE | RECOMMENDED ACTION |
Motor does not start. | No power to motor. | Check wiring and power from primary control lead. If necessary, replace control, limit controller, or fuses (time-delay type). |
Insufficient voltage supply. | Check power from primary control. | |
Thermal protector has tripped. | Determine and repair cause of thermal overload – bound pump or ambient too high. | |
Fuel Pump seized. | Disconnect motor from pump. Turn pump shaft by hand checking tightness. | |
Capacitor or windings have failed. | Check capacitor and windings (see above). | |
Motor bearings have failed. | Turn the motor shaft, which should turn easily. | |
Motor starts but does not reach full speed. | Motor is overloaded. | Disconnect pump from motor. Turn pump shaft to ensure free rotation. |
Insufficient voltage supply of low frequency. | Check power from primary control. Voltage should be 110 – 120 Vac at 60 Hz. | |
Capacitor or windings have failed. | Check capacitor and windings (see above). | |
Motor vibrates or is noisy. | Bearings are worn, damaged, or fouled with dirt or rust. | Replace motor. |
Motor and pump are misaligned with each other or housing. | Check pump and motor to ensure that they are seated in the housing properly. | |
Blower wheel or wheel balancing weight (if applicable) is loose. | Check blower wheel and balancing weight (if applicable) for location and tightness. | |
Motor draws excessive current (>10% over rated current). | Motor and pump misaligned with each other or housing. | Check pump and motor alignment to housing. Check coupling length – too long will bind. |
Fuel Pump seized. | Check pump model to make sure it is correct; turn pump shaft by hand, checking tightness. Check pump pressure to make sure it is set within the specification | |
Motor windings are damaged. | Check windings (see above). If damaged, replace motor. |
Informative and technical training resources from the leading experts in the heating industry
Have questions about our products? Looking for a solution to address a particular application? Looking to improve the overall productivity and profitability of your operation? Please don’t hesitate to reach out or schedule a no obligation, 1-on-1 consultation with a Beckett Technical Specialist — we’d love to help.
Beckett solutions are available through our network of Distributors, Independent Representatives, and Export Representatives all around the world.