×
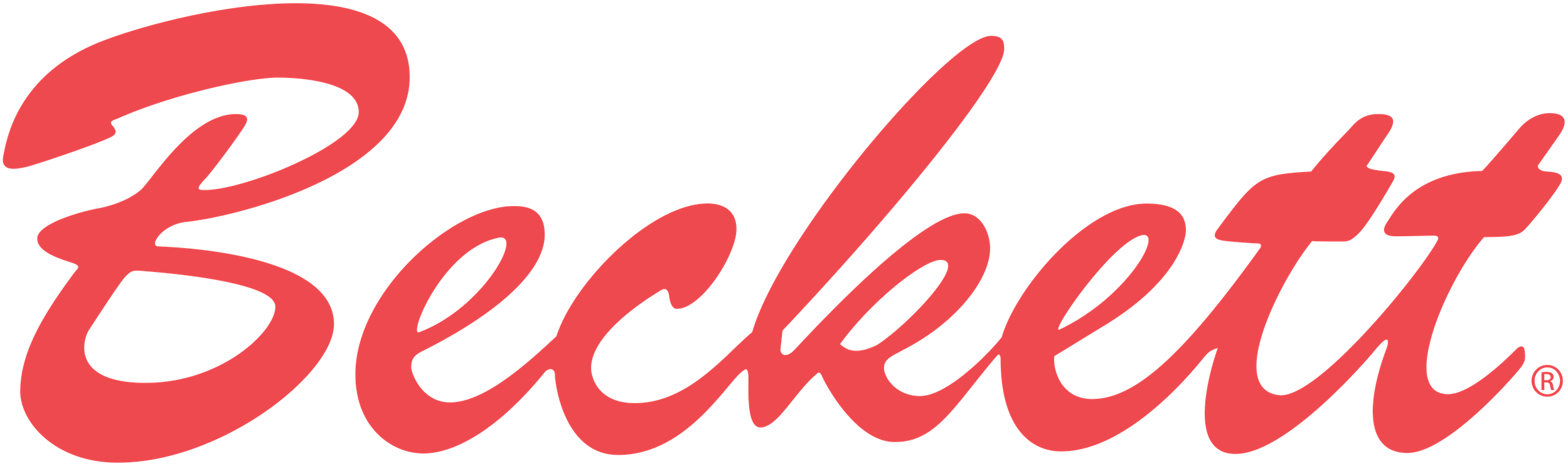
Regional Sales Manager Request
Please fill out the form below to contact Beckett directly and we’ll get back to you within 24 hours.
In the oil heating industry, “draft” describes the vacuum, or suction, which exists inside most heating systems. The amount of vacuum is called draft intensity. Draft volume specifies the cubic feet of gas that a chimney can handle in a given time. Draft intensity is measured in “inches of water”. Just as a mercury barometer is used to measure atmospheric pressure in inches of mercury, a draft gauge is used to measure draft intensity (pressure) in inches of water.
Natural Draft is thermal draft. It occurs when heated gases expand. A given volume of hot gas will weigh less than an equal volume of the same gas at a cool temperature. Since hot combustion gases weigh less per volume than room air or outdoor air, they tend to rise. The rising is contained and increased by enclosing the gases in a tall chimney. The vacuum is then created throughout this column of hot gases.
Currential Draft occurs when high winds or air currents across the top of a chimney create a suction in the stack and draw gases up. “Induced draft” blowers can be used in the stack to supplement natural draft where necessary.
There are three factors which control chimney draft:
Since the outside temperature and flue gas temperature can change, the draft will not be constant. When the heating unit starts up, the chimney will be filled with cool gases. After the heating unit has operated for a while, the gases and the chimney surface will be warmer, increasing draft. As outside air temperature drops, draft
increases. To indicate the effect of these changes, the information in the chart on page 2 was determined for a 20 foot high chimney. You can see that the draft produced by this chimney could be expected to vary from .011 to .136 inches of water. The high draft is over 12 times more than the low draft. This large variation cannot be tolerated for the following reasons:
To understand these problems, consider that the air pressure (positive draft) caused by a flame retention burner fan averages about .40 inches of water in the air tube. If the combustion chamber has a draft of .10 inches of water, the total force causing air to flow will be .50 inches of water. If the combustion chamber draft drops to .01 inches of water, the total pressure becomes .40 +.01, or .41 inches of water.
This is a reduction in draft of about 18% which will cause a reduction in the amount of air flowing into the combustion chamber. You know what happens when the excess air is not properly adjusted. The burner may very likely smoke as a result of this change. That is why proper draft must be obtained before the air adjustment is set.
Because there is little draft during a cold start-up, you cannot depend on the additional combustion air caused by draft. Be sure the burner does not depend on this air by setting the burner for smoke-free combustion with a low over-fire draft (.01 to .02 inches of water). A burner must produce good smoke-free combustion under low draft conditions. Using a high draft setting to obtain enough combustion air for clean burning can cause trouble. A burner which produces clean combustion only with high draft may cause smoke and soot any time the chimney is not producing high draft.
Condition | Outside Temperature °F | Chimney Temperature °F | Draft, “H₂O” |
Winter start up | 20 | 110 | .050 |
Winter operation | 20 | 400 | .136 |
Fall start up | 60 | 80 | .011 |
Fall operation | 60 | 400 | .112 |
Informative and technical training resources from the leading experts in the heating industry
Have questions about our products? Looking for a solution to address a particular application? Looking to improve the overall productivity and profitability of your operation? Please don’t hesitate to reach out or schedule a no obligation, 1-on-1 consultation with a Beckett Technical Specialist — we’d love to help.
Beckett solutions are available through our network of Distributors, Independent Representatives, and Export Representatives all around the world.