×
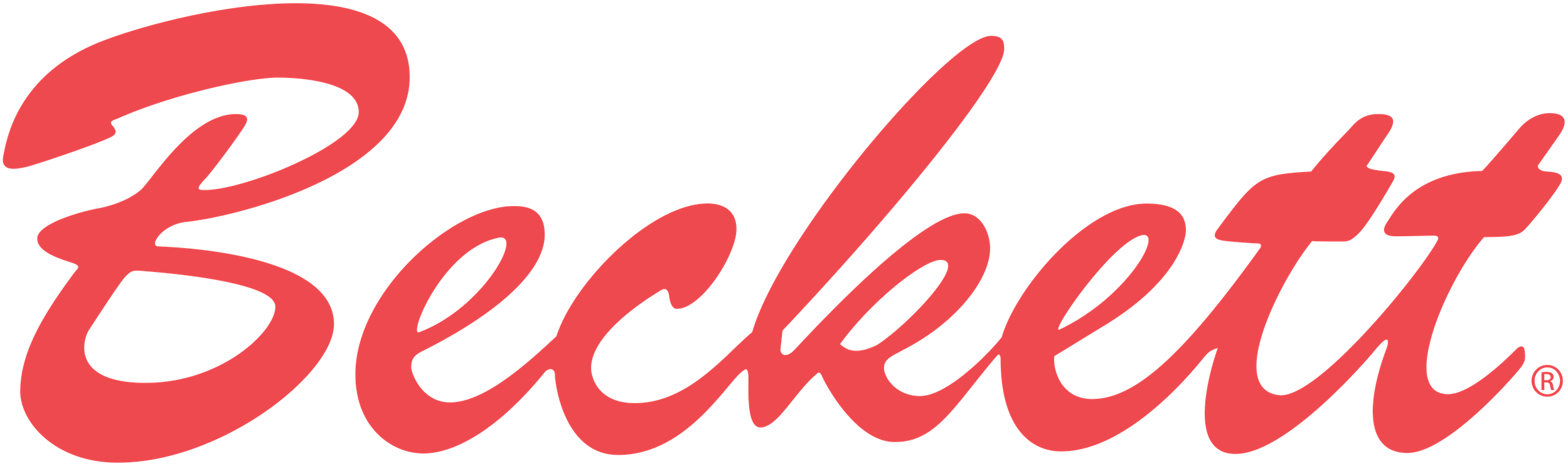
Regional Sales Manager Request
Please fill out the form below to contact Beckett directly and we’ll get back to you within 24 hours.
Much has been written about the quality of fuel oil in recent years. Some feel that at times oil can cause service problems. So, let’s consider some pertinent facts about residential fuel oils, including a close look at specifications and properties that affect burner operation.
There are variations within each grade of fuel oil. The American Society for Testing Materials (ASTM) has developed standards and testing methods that enable laboratories to make uniform analyses of fuel oil properties. These properties for No. 2 fuel oil include: specific gravity, flash point, pour point, viscosity, distillation temperature, sulfur content, corrosion, carbon residue, water and sediment.
While all of these properties are very important, we will focus upon the ones that most commonly impact on residential oil burner performance.
Oil viscosity can be simply defined as the measure of the oil’s resistance to flow. The Saybolt Universal viscosimeter uses a standard orifice, controlled amount of oil and measure of time elapsed for the sample to flow through at 100°F. The total number of seconds required is the viscosity rating. The ASTM D396 Standard permits a maximum rating of 37.9 SUS (Saybolt Universal Seconds) and 32.6 SUS minimum.
Oil that exceeds this upper limit of 37.9 SUS can contribute to poor atomization, delayed ignition, noisy flame or pulsation, increased input and possible sooting of the appliance. These conditions become amplified as the ambient temperatures drop below 50°F. (See Figure 1.)
Sometimes viscosity is measured by the Kinematic voscosimeter and is reported in centistokes. See Figure 2 for cross-reference.
The temperature at which an oil will barely flow under controlled test conditions is the pour point. This is usually 5ºF above the temperature at which the oil thickens into a solid mass. The ASTM D396 Standard lists the maximum pour point at 20°F. Obviously, if this range is exceeded, there could be problems with oil flow in certain cold ambient applications. Generally, when this is encountered, the No. 2 fuel oil is blended with approximately 25% No. 1 distillate fuel (Kerosene) to effectively lower the pour and cloud points.
The cloud point is the temperature at which wax crystals begin to form in the oil sample. This typically ranges from 20-35°F above the pour point. When the cloud point is reached and exceeded in practice, wax crystals can form and clog filters and strainers thus causing restriction of oil flow. When the oil temperature is raised, the wax goes back into solution. The ASTM D396 Standard does not have a specification for the cloud point.
One of the more important properties of No. 2 fuel oil is its distillation temperature. It can be vaporized and distilled at atmospheric pressure when heated to 650-700°F. However, modern refinery methods produce fuel oil through straight-run distillation and catalytically cracked processes. This results in slightly different chemical hydrocarbon composition and can affect combustion performance. Therefore, the distillation temperature test is valuable. It requires that a controlled amount of fuel oil be heated gradually in a glass container. As oil is vaporized, it leaves the flask and enters a condenser, becomes liquefied and is collected in a graduated cylinder. The temperature at which the first droplet is condensed is the initial boiling point (IBP). The temperature continues to rise and is recorded for each fraction distilled. This is usually reported in 10% increments until the final drop is recovered or end point is reached.
The initial boiling point could create ignition problems if it is too high (over 400°F). The ignition arc must provide enough heat energy to elevate the temperature of the atomized oil droplets to the initial boiling point. If the IBP is low, then ignition should be immediate. For the flame to be sustained, the 10% point or temperature at which 10% of the total volume is distilled must be relatively close. If the spread is too large, then the flame could pulsate or even be extinguished. Interestingly, the IBP and 10% point are not specified in ASTM D396 Standard for No. 2 fuel oil.
Once the flame has been established, the remaining fractions of 20-80% should not present any combustion problems, but the 90% and the end point could. The 90% point is the temperature at which 90% of the oil is distilled. The ASTM D396 Standard requires this range to be within 540°F minimum and 640°F maximum. If the spread between the 90% point and end point is large, then the remaining heavy ends may not burn completely, thus possibly causing poor combustion, soot and carbon deposits on the heat exchanger.
From our brief discussion, we can see that the refining of fuel oil is a complex process and numerous factors can affect the performance of residential oil burning equipment.
The oil entering our marketplace comes from various global regions. The refining processes can differ from catalytically cracked to straight-run distillation and blending of oils to meet grade specifications. This can cause wide variations in the final product.
Historically, residential fuel oil has been very uniform with few problems encountered. The ASTM specifications were essentially adhered to. However, there are those occasions when oil does not meet the specifications. The oil dealer or service agency must be alert for these conditions. For example, there could be a sudden upsurge in service problems that had not been encountered previously, such as: delayed ignition, smoky fires, appliance sooting and flames that are noisy and difficult to clean up. Here an oil sample for analysis by a competent laboratory might be advisable.
If the sample analysis reveals that the oil is “out of specification,” the matter should be brought to the attention of the supplier. On the other hand, if the oil is within specifications, but is marginally close to the maximum levels for either viscosity, pour point or above 400°F. IBP, then chemical additives or blending with about 25% Kerosene might be considered. This action should certainly make the oil more suitable for cold ambient conditions and contribute to improved ignition and combustion characteristics.
In the meantime, we must count on the integrity of suppliers, and random analyses when necessary, to help our industry keep oil quality problems to a minimum.
Informative and technical training resources from the leading experts in the heating industry
Have questions about our products? Looking for a solution to address a particular application? Looking to improve the overall productivity and profitability of your operation? Please don’t hesitate to reach out or schedule a no obligation, 1-on-1 consultation with a Beckett Technical Specialist — we’d love to help.
Beckett solutions are available through our network of Distributors, Independent Representatives, and Export Representatives all around the world.